Understanding What is Porosity in Welding: Causes and Solutions
Understanding What is Porosity in Welding: Causes and Solutions
Blog Article
The Scientific Research Behind Porosity: A Comprehensive Guide for Welders and Fabricators
Recognizing the detailed mechanisms behind porosity in welding is vital for welders and makers striving for remarkable craftsmanship. As metalworkers explore the depths of this phenomenon, they reveal a globe controlled by numerous elements that influence the development of these minuscule gaps within welds. From the composition of the base products to the complexities of the welding procedure itself, a wide variety of variables conspire to either exacerbate or ease the presence of porosity. In this extensive guide, we will certainly untangle the science behind porosity, discovering its effects on weld high quality and introduction advanced strategies for its control. Join us on this journey via the microcosm of welding imperfections, where accuracy satisfies understanding in the quest of flawless welds.
Understanding Porosity in Welding
FIRST SENTENCE:
Evaluation of porosity in welding exposes vital insights right into the honesty and top quality of the weld joint. Porosity, defined by the presence of dental caries or voids within the weld steel, is a common problem in welding procedures. These spaces, if not correctly dealt with, can jeopardize the structural integrity and mechanical homes of the weld, leading to potential failures in the ended up product.
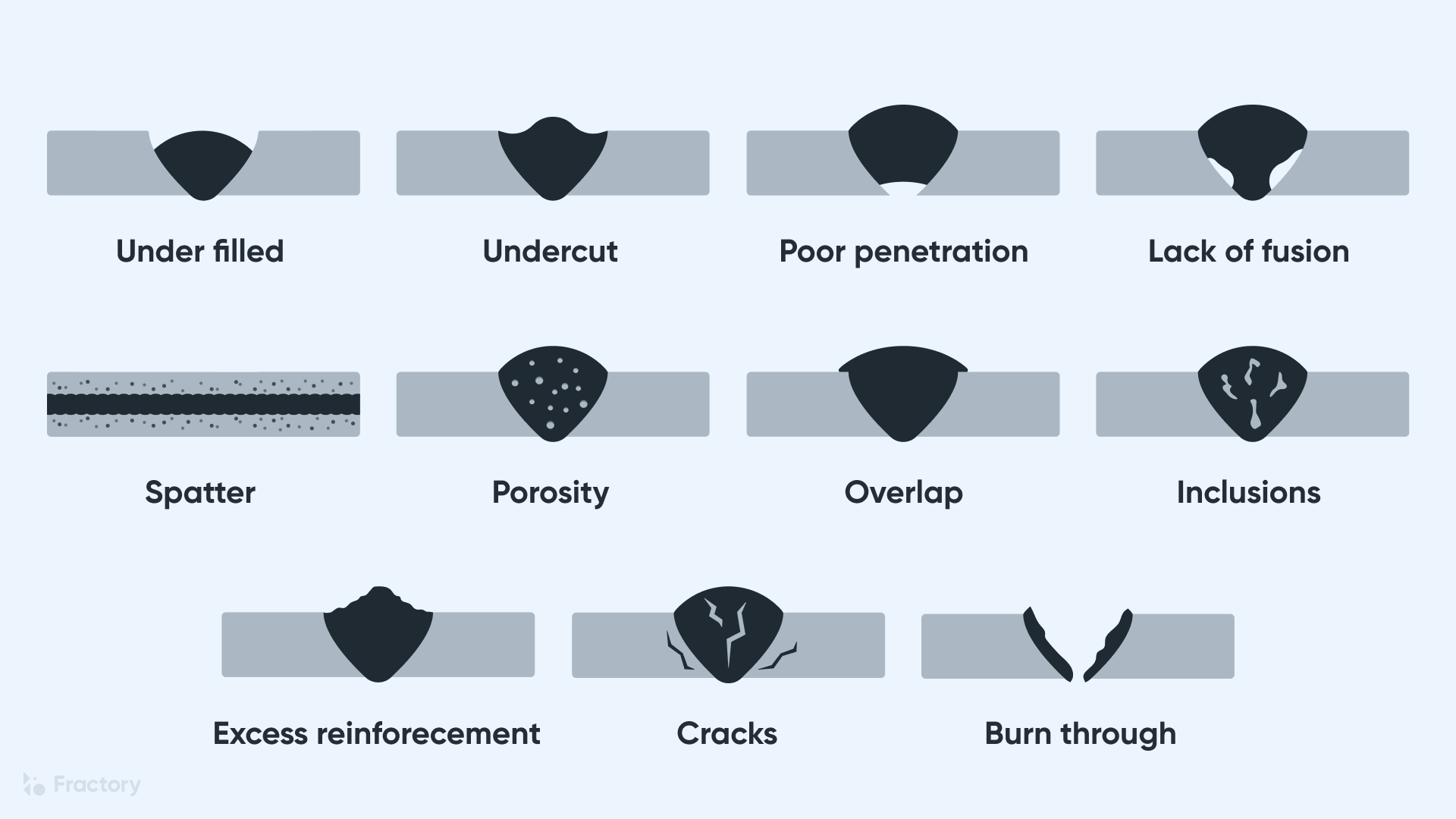
To spot and quantify porosity, non-destructive testing methods such as ultrasonic screening or X-ray inspection are often utilized. These methods enable for the recognition of inner defects without compromising the honesty of the weld. By evaluating the dimension, form, and circulation of porosity within a weld, welders can make educated decisions to boost their welding processes and achieve sounder weld joints.

Factors Affecting Porosity Formation
The incident of porosity in welding is affected by a myriad of aspects, ranging from gas securing effectiveness to the details of welding specification settings. Welding criteria, including voltage, existing, travel rate, and electrode type, additionally effect porosity development. The welding method employed, such as gas metal arc welding (GMAW) or secured steel arc welding (SMAW), can influence porosity formation due to variants in heat circulation and gas coverage - What is Porosity.
Impacts of Porosity on Weld Top Quality
The visibility of porosity likewise weakens the weld's resistance to corrosion, as the caught air or gases within the spaces can react with the surrounding environment, leading to destruction over time. In addition, porosity can prevent the weld's ability to endure pressure or influence, additional jeopardizing the total high quality and dependability of the bonded framework. In vital applications such as aerospace, automotive, or architectural buildings, where safety and durability are extremely important, the damaging results of porosity on weld high quality can have severe effects, emphasizing the relevance of lessening porosity through appropriate welding techniques and treatments.
Techniques to Decrease Porosity
In addition, making use of the appropriate welding specifications, such as the right voltage, existing, and take a trip speed, is essential in avoiding porosity. Preserving a constant arc length and angle during welding likewise assists minimize the chance of porosity.

Furthermore, picking the check right shielding gas and maintaining proper gas flow prices are essential in minimizing porosity. Using the appropriate welding technique, such as back-stepping or employing a weaving motion, can also aid disperse warmth equally and minimize the possibilities of porosity development. Ensuring correct air flow in the welding atmosphere to eliminate any possible resources of contamination is crucial for accomplishing porosity-free welds. By executing these techniques, welders can properly lessen porosity and create top quality welded joints.
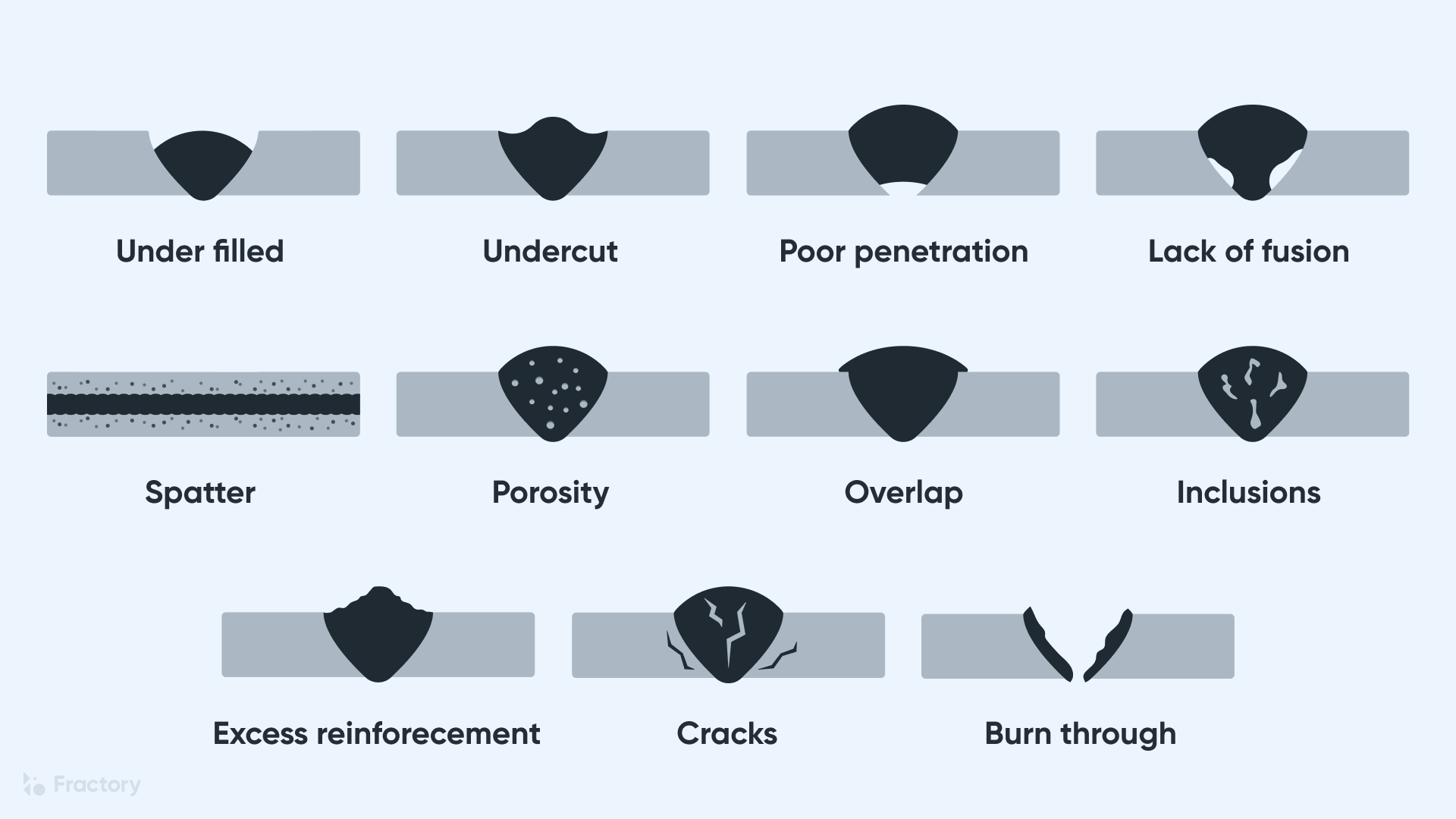
Advanced Solutions for Porosity Control
Applying advanced modern technologies and innovative techniques plays a critical duty in achieving remarkable control over porosity in welding processes. In addition, utilizing sophisticated welding strategies such as pulsed MIG welding or customized atmosphere welding can additionally aid mitigate porosity problems.
One more advanced solution includes making use of advanced welding equipment. Using equipment with built-in features like waveform control and sophisticated power sources can improve weld high quality and minimize porosity risks. In addition, the execution of automated welding systems with precise control over parameters can considerably reduce porosity flaws.
Additionally, incorporating advanced monitoring and inspection technologies such as real-time X-ray imaging or automated ultrasonic testing can help in finding porosity early in the welding process, permitting prompt rehabilitative activities. In general, integrating these sophisticated services can substantially enhance porosity control and enhance try this out the total high quality of welded components.
Verdict
To conclude, understanding the scientific research behind porosity in welding is necessary for welders and makers to create top quality welds. By identifying the variables influencing porosity visit our website formation and executing strategies to lessen it, welders can improve the overall weld top quality. Advanced options for porosity control can even more boost the welding process and ensure a strong and reliable weld. It is vital for welders to continually inform themselves on porosity and implement finest methods to attain optimal results.
Report this page